SOLVE YOUR EMULSION PROBLEM BY REDUCING YOUR COSTS AND INCREASING YOUR PRODUCTIVITY
About us
- History
- Election of the mixer
- Tipe of equipement
The first colloidal mills was made in Germany in the decade 30. Originally were rotor of several stages and
always its design was conical. In the decade 70 it improve the design to rotors/stators of a single stage. The
materials used for their manufacture are stainless steel AISI 316, being able to use steel temperings that increase
to double their duration for the rotor/stator.
The colloidal mills are used generally to make emulsions. The manufacture can also be about to enrich the phase
of dispersion gradually. The basic principle consists of the action that produces a rotor fluted when turning to 3,000
rpm to count a fixed stator also fluted, being put under the product to process to strong actions of cut and friction.
The cones of special design are constructed in steel, chromium nickel, stainless steel 304 or 420 templables. The
regulation of the cones takes place by means of a steering wheel that allows to graduate the separation and
approach between the cones. The design of a centrifugal disc makes the effect of pump impelling the product
through pipes being able elevate it until a certain height working the mill like pump.
The specific result to be achieved with the mixture must be taken into account. Thus, an
agitator that is satisfactory to stimulate dissolution of soluble solids in a liquid may not be effective in maintaining
insoluble solids in a uniform suspension.
In many cases, the agitator may be needed to perform two or more simultaneous functions:
Good contact between immiscible liquids and at the same time, has to stimulate the effective transmission of heat
inside the material and from it.
The selection of the appropriate mixer will also depend on the medium in which it is to be worked; be it a gas, a
liquid or a mass of solid particles; either homogeneous or heterogeneous with respect to the phases; or the phases;
either high or low consistency.
The design of an agitator requires the specification of the type of apparatus, the dimensions and proportions of the
mixing element, the location of this element within this vessel for mixing and the operating conditions of the agitator.
In general, the optimal mixer, as well as the optimal equipment for other unit operations, will be the one that
achieves the desired result with the most economical combination of fixed and operating loads.
In practice, the disperser is usually selected to ensure more effective results and to be more attractive from the
standpoint of its installed cost and its conservation, since the energy consumed in the mixture is frequently only a
small part of that required for all the process.
However, the meticulous designer will investigate the energy needs, particularly in operations that require high
power dispersers. The type, or types, dimensions and position of the agitator for the operation are first determined
from the general empirical principles. Then the operating conditions are specified; these are less easy to generalize
and are deduced by the experience of the engineer or the equipment vendor, or by means of model tests.
Although there is a wide variety of mixers and dispersers on the market, these can be divided
into low and high cutting applications. In the form, typically paddles or type propellants, the reduction of the size of
the particle does not take place, the action is carried out by the melting and / or dissolution.
The mixer serves to maintain the homogeneity of the composition and the uniformity of the temperature, providing a
small increase in itself. In the latter case, there is a step in which the particles are physically reduced in size by
mechanical / hydrodynamic cutting with the rotor / stator combination accompanied by a small increase in
temperature by the mixing energy.
Such equipment, even when working with particles larger than pellets, provides fast and efficient dispersion and
mixing.
Equipment of high effort of cutting exist of two different ways, type immersion vertical and the one of the mixed in
line.
* The vertical, the rotor / stator is mounted on a platform and immersed in a tank of material, depending on the
mixing head to circulate the mixture and ensure homogeneity.
* The case of mixing in line, the combination of mixing in a tank recirculating by a pump mill.
Experiences have shown that this type of equipment, which ensures total dissolution, gives greater speed and
performance than disintegration with a single vertical mixer, especially for large production volumes, tanks greater
than 25 tons.
LOOKING FOR AN ADEQUATE SOLUTION FOR YOUR COMPANY?
Technical characteristics
- Available rotors: Normal teeth, crossed
- Mounting: On mobile or fixed base, for operation in vertical, horizontal or both.
- Shaft connection: Acrylic-nitrile gaskets, Viton or mechanical seal.
- Construction: According to strictly sanitary regulations.
- Electric motor: IP 65 three-phase asynchronous motors, on request anti-explosive.
- Protection: Stainless steel protection motor housing.
- Material: Stainless steel AISI 304, 316, 420 or 430 with leakage certificate
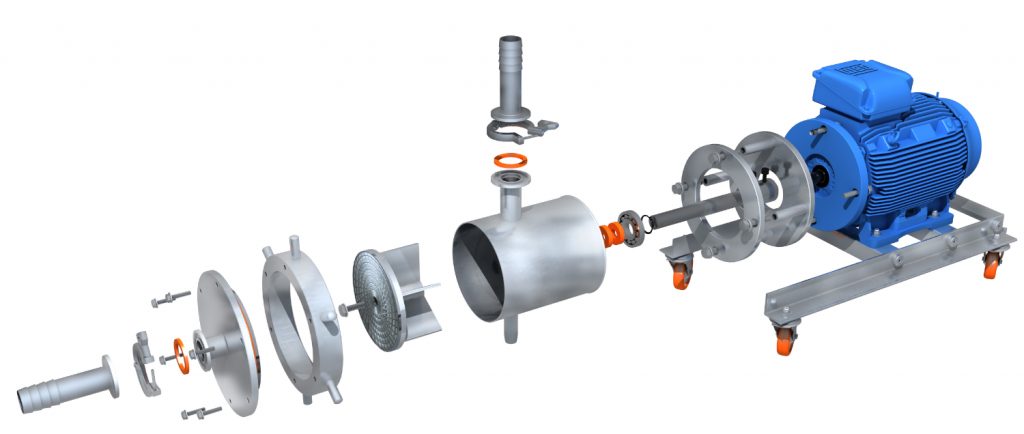
Colloidal Mill
Solve your emulsion problem by reducing your costs and increasing your productivity
contact information
- +54 114754 - 9374
- + 54 11 6351 6288
- info@colloidalmill.com
- Calle 28 3332 - San MartÃn, provincia de Buenos Aires - Rep. Argentina
social media
All right reserved – Colloidal Mill
Web design nicolasjpereira